Lasergrammetry
Laser scanning is a modern technique which has generated much new terminology. Several different expressions may be encountered covering the technique itself.
- laser scanning, laser scanner : the accepted general terms for the technique and the instrument respectively, both for terrestrial and airborne applications ;
- lidar : “light detection and ranging”, interchangeable with laser scanning, laser scanner, especially in airborne applications ;
- High-Definition Surveying : term introduced by Leica Geosystems in connection with their HDS “family” of laser scanners and software as used by TPLM-3D ;
- lasergrammetry : we commonly use lasergrammétrie in France, especially for terrestrial applications, but we acknowledge that this is not in general use in English nor internationally because laser scanning has been treated as an innovation within the existing discipline of photogrammetry, rather than as a new discipline in itself ;
- laserometry : has occasionally been used in English language texts, but we understand not generally by native speakers ! Laserométrie is sometimes used in French for industrial applications ;
- “bombardement laser” : term much used in Switzerland and Belgium, but avoided in English for measurement applications because of at least three very different alternative connotations of “laser bombardment” !
Laser scanning terminology
Laser scanning is a modern technique which has generated much new terminology. Several different expressions may be encountered covering the technique itself.
- laser scanning, laser scanner : the accepted general terms for the technique and the instrument respectively, both for terrestrial and airborne applications ;
- lidar : “light detection and ranging”, interchangeable with laser scanning, laser scanner, especially in airborne applications ;
- High-Definition Surveying : term introduced by Leica Geosystems in connection with their HDS “family” of laser scanners and software as used by TPLM-3D ;
- lasergrammetry : we commonly use lasergrammétrie in France, especially for terrestrial applications, but we acknowledge that this is not in general use in English nor internationally because laser scanning has been treated as an innovation within the existing discipline of photogrammetry, rather than as a new discipline in itself ;
- laserometry : has occasionally been used in English language texts, but we understand not generally by native speakers ! Laserométrie is sometimes used in French for industrial applications ;
- “bombardement laser” : term much used in Switzerland and Belgium, but avoided in English for measurement applications because of at least three very different alternative connotations of “laser bombardment” !
Principles of laser scanning
Laser scanner surveys are similar to three-dimensional photographs of the measured object. The position of every scanned point is immediately known in 3D Cartesian coordinates X, Y, Z. From the surveyor’s point of view, there is a radical change of philosophy compared with traditional surveying : we now survey the object in its entirety, rather than merely its characteristic features. The accuracy of such a system can be illustrated by the standard deviation for each observed point. However, the accuracy of the modelled result can be better than the accuracy of the raw data, because of the very high density of the observations and the consequent high degree of redundancy. If you require information at high resolution, opt for this technology!
Definition of a 3D laser-scanning system
For the user, a 3D laser-scanning system is an instrument which measures the 3D coordinates of points across an area on the surface of an object
- automatically and systematically,
- at high speed (tens or even hundreds of thousands of points per second),
- while enabling the acquisition of these coordinates in real time.
For each point a scanner may also provide
- a value which is a function of the reflectivity of the object, and
- RGB values obtained by a digital camera.
3D laser scanners may be used
- in fixed positions (e.g. for industrial quality control),
- by moving between instrument stations (terrestrial scanner used for topographic or engineering applications), or
- in mobile applications, mounted on a vehicle, or airborne, in conjunction with an on-board navigation system.
Important considerations in the choice of a laser scanning system
For a laser scanner to be fully effective for its required purpose, it is important to consider the following :
- the associated post-processing software ;
- the accuracy of the system (generally expressed as the standard deviation of each point) ;
- the size of the laser spot as a function of the object distance ;
- the maximum and minimum range of the instrument ;
- the scanning rate (expressed in points per second, from 50’000 to 1’000’000 depending on the instrument) ;
- the angular field of view ;
- the site environment (temperature, humidity, radioactivity, etc.) ;
- ease of use (weight of the equipment, for example) ;
- power supply requirements ;
- laser safety considerations (some early systems required sites to be cleared of personnel during measurement) ;
- the instrument manufacturer.
The Z+F IMAGER 5016
The Z+F IMAGER 5016 is a compact, portable terrestrial 3D laser scanner weighing just 7 kg. It offers a range of 360 m and an acquisition speed of 1 million points per second, guaranteeing high accuracy even over long distances.
Its 360° x 320° field of view provides optimum coverage, reducing the number of scan positions required. It is equipped with an 80 MP HDR camera and LEDs, ensuring sharp images even in low-light conditions.
An integrated positioning system enables forward consolidation directly in the field, with or without targets. Its rugged design (IP54) makes it water and dust resistant, with an operating range from -10°C to +45°C.
It is ideal for applications requiring accurate, efficient 3D scanning.
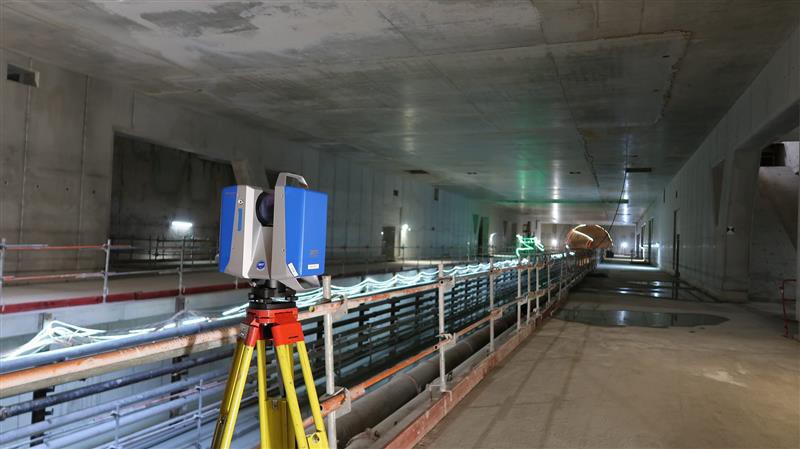
The Zoller & Fröhlich Imager 5010 C system
This system is based on measuring the phase shift between transmitted and received waves. With ranges from 30 cm to 187 m, it can be used almost universally on all types of worksite.
Its IP 53 classification, without ventilation, and its compact size make it the system of choice for surveys in nuclear environments.
What's more, thanks to the on-board coaxial HDR camera, we can easily generate colorized point clouds and 360° color panoramas, without the need for an external system.
The measurement noise of the Zoller & Fröhlich Imager 5010 C is among the lowest on the market, particularly on objects such as piping and steelwork: it's 0.4 to 0.8 mm in the range of ranges we use.
Key features :
- phase shift;
- on-board HDR color;
- up to 1 Mio points / second;
- 360° horizontal × 320° vertical;
- range from 0.3 m to 187 m.
The Leica HDS6100 scanner system
TPLM-3D has invested in a new generation of scanner, the HDS6100 system, to carry out surveys where the availability of the site, or the window of opportunity to operate, is extremely short (during planned shutdowns, for example). This system is based on phase comparison between the emitted and the returned pulses. In operation, a continuously spinning horizontal cylinder deflects the laser beam in the vertical plane, the whole being mounted on a base rotating in the horizontal plane. Minimum and maximum ranges are 1 m and 79 m respectively. The field of view of the HDS6100 is 360° (horizontal) and up to 310° (vertical). This state-of-the-art system is ideally suited to surveys in the nuclear environment for several reasons :
- IP 50 rating ;
- it can very easily be wrapped in vinyl and still be operated ;
- it is very compact.
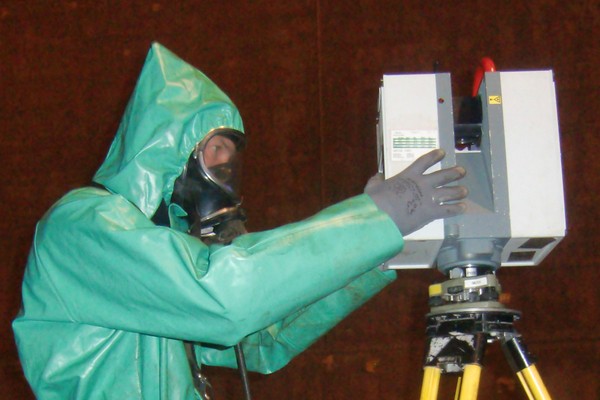
The main features of laser scanner surveys using this technology are :
- speed of data capture up to 500’000 points per second ;
- density of information of the order of one point per 5 mm ;
- direct capture of three-dimensional data on site ;
- measurement accuracy (6 mm at 25 m, 10 mm at 50 m on every point).
Post-processing of laser scanner data
Our special software enables us to extract surfaces, edges, solid figures, lines and points and then to model the objects in 3D. Alternatively, 2D data (cross sections, elevations, plan views) can also always be extracted. All of these plots and models can then be supplied to you in standard CAD formats.